

"Kuhn Rikon": How a metal disc becomes a cooking pot
The village of Rikon is already in the name of the company: "Kuhn Rikon" stands worldwide for high-quality pans, a large part of which have been "Made in Rikon" for almost a hundred years. I was allowed to follow the creation of a pan from design to finished product.
Did I fall asleep for a moment on the train? Just ten minutes ago we were in Winterthur, the second largest city in the canton of Zurich. Now the train stops in Rikon and it looks like we are in Emmental or Toggenburg. A river meanders parallel to the railroad line further down the valley. To the left and right are rolling, wooded hills. The village is so small that I can't miss my destination. The "Kuhn Rikon" pan factory has been producing pots and pans for the whole world here in an industrial building right next to the train station since 1926. Since the 1950s, so many Swiss kitchens have been equipped with the "Duromatic" pressure cooker that its name is still used today as a synonym for all pressure cookers. Today, the company, now in its fourth generation of family ownership, has 200 employees and sells its products in over 30 countries.
While the "Duromatic" pressure cooker popularized the old concept of pressure cooking in Switzerland, another pride of the company is the "Durotherm" pan. An invention of the founder's son Jacques Kuhn. As a bachelor, Jacques liked to cook for guests and preferred to enjoy the aperitif with his visitors instead of standing in the kitchen stirring in pots. The engineer therefore developed a cooking pot that would keep the food warm for a long time, so that he could duly fulfill his role as host. The principle is simple: the pan and lid have a double wall, and the layer of air between the walls insulates and keeps the food in the pan warm (or cold, if desired).
Since its invention in 1975, nothing has changed in this basic concept; even today, the double wall provides insulation. Design and materials, however, are always being adapted and move with the times.
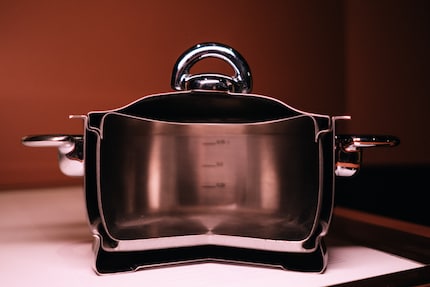
Tinkering in the beginning
Michael Hörth has been working as a design engineer at "Kuhn Rikon" for ten years. He sits behind four 3D printers in an office. Where there are federal folders or paper trays in the accounting department, there are piles of pans, lids and handles of all sizes and shapes. Among them, a "Durotherm" with unsightly discolorations. "Such discolorations can occur especially on induction stoves. The material cannot withstand the high heat," Hörth explains. Discolored pans are usable without any problem, but they are not nice to look at. The phones at customer service have been ringing off the hook for the last few years, and a solution was needed.
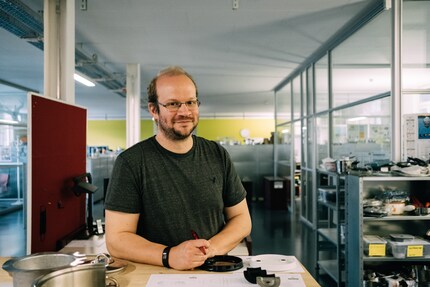
"Until we found a new material, we had to fiddle around for a long time. Together with universities, we finally came up with a multilayer alloy," says Hörth proudly. Months of testing and trial and error were carried out - including with friends and family. "My father is a chef and therefore from the trade. He helps test the prototypes. That's what I like about my job, people are creative with these products later, they create something with them," Hörth explains. Previously, he had worked in medical technology. There, the execution was subject to strict rules and specifications. "Now I have a say in how the products come off the conveyor belt at the bottom."
A disk becomes a cylinder
Downstairs, that is the production of "Kuhn Rikon". Several halls in which blanks are drawn, ground, polished, assembled and packaged as finished pans. An employee wearing hearing protection and safety goggles places a round metal disc in the hydraulic press and pushes a button. The press closes with a loud hiss. When it opens again a few seconds later, the disk has been formed into a cylinder. The shape reminds me of the hat of a magician who amazes children with a few card tricks. He stoically checks that there have been no cracks and clamps the blank into the next machine, which cuts off the edge of the magician's hat with a loud "clack".
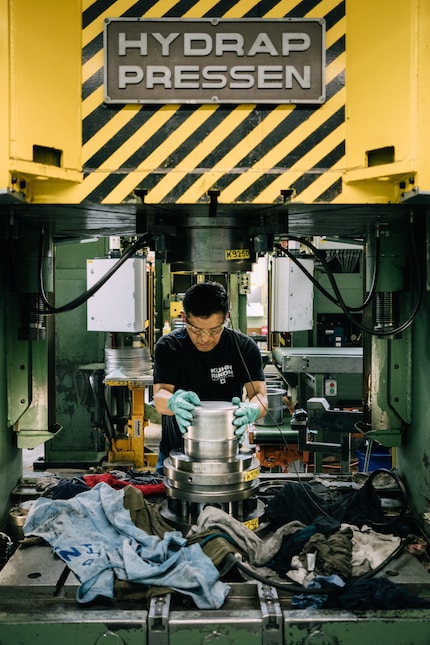
Now it is clearly visible that the round blank will later become a pan. With a cloth, the employee wipes off the remaining lubricant and grabs the next slice. Hiss. Clack. Hiss. Clack. Over and over again. The machine has to run at least two thousand times before it is converted to another pan size, otherwise the effort is not worth it.
How a designer from New York came to Rikon
One floor up in the office, colorfully printed A3 pages hang on a wall. It is a look into the future. This is what the pots and pans from "Kuhn Rikon" should look like in the next few years. I am sitting at the workplace of Jochen Schaepers, industrial designer at "Kuhn Rikon" for two years. "After 25 years as a freelancer in New York City, it's a stark change. But a change that has paid off," says Schaepers. He moved to Switzerland for love. "My wife works in the pharmaceutical industry and took a job in the Basel region. That's where I'm with."
In New York, the German-born Schaepers consulted for companies. He made suggestions about what products from startups might look like. "Whether and how the customers then implemented the ideas, I had no influence on that. Here, on the other hand, I'm involved from A to Z, from the first sketch to the finished product. I like that." Doesn't he become a control freak here, monitoring every step? Schaepers ponders for a moment. "My wife would say, yes!" to immediately add that the designs are created together as a team and they don't come from his pen alone.
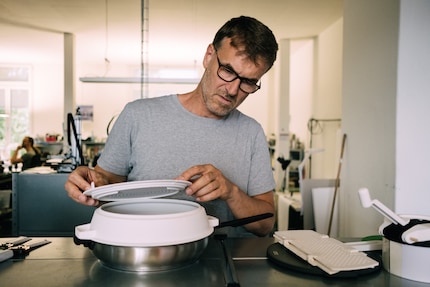
In the five-person team, everyone has an equal say. That wasn't always the case: "When I started, everyone had their own projects. This way of working had the disadvantage that the designs didn't come from a single mold, because everyone had their own style." However, products from "Kuhn Rikon" should be recognizable to the customer at first glance. "For example, this lid of the new Durotherm pots." Schaepers shows me over a dozen printed 3D images of lids with different handles. Sometimes square, sometimes round, sometimes with a hole, sometimes without a hole. In addition, some of the designs lie in front of us as 3D prints next to older models. "You can clearly see here how we tried to take up the old design again," Jochen Schapers enthuses, and I am fascinated by how much passion goes into such a banal object as a pot lid.
The pot gains ground
Meanwhile, in production, the bottom of our blank has grown thick. A machine soldered a round, centimeter-thick aluminum disk to the bottom under great heat. Not much could be seen of the process. The pan blank with the thin bottom has been clamped in a box and after half a minute had a thick aluminum bottom.
An employee is now tampering with the freshly soldered-on ladle bottom with some kind of jackhammer and is desperately trying to remove it, which only works with great difficulty. Has something gone wrong? Assembly manager Mathias Schneider laughs: "No, hopefully not! This is quality assurance. We let a few thousand pots through during this shift. If the machine is set up incorrectly somewhere, we can throw them all into the scrap metal. So it's important to check the first few pots after welding."
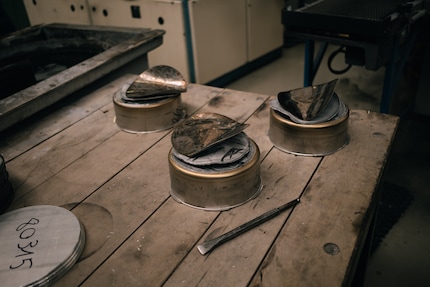
The broken bottoms lie there like autumn leaves, and everything is meticulously documented. If the bottom comes off the blank too easily, the soldering machine would have to be readjusted. In this case, that is not necessary and the employee starts production.
"This machine polishes the pots quite automatically in several steps," says production manager Schneider to the next station, a few meters away. There stands a huge cube, the size of an average room. The dull, dirty blanks go in on one side and leave the cube polished to a high gloss on the other. I don't see exactly how this works. The cube has hardly any windows, so I can't see anything through them.
Cameras are supposed to show what is happening inside the polishing unit, though I can only make out abstract, colored outlines. They are thermal cameras that an employee checks on a monitor to make sure the pots don't get too hot during polishing. That can happen quickly because the polishing wheels rub against the blanks at high speed. "We had a fire in this machine in 2015, everything was destroyed. For months, we had to outsource polishing and buy a new machine," Schneider explains. Millions of euros in damage was the result. Trust is good, control is better.
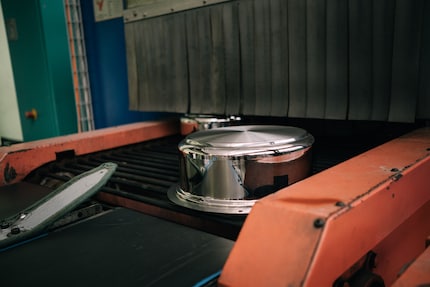
The tool here weighs tons
Meanwhile, in the design department, chief designer Schaeper shows me the new lid. "The highlight of it is that the handle is embedded in the top of the lid". What I don't notice as a layman is the result of a months-long design process. Industrial design, engineering department and toolmaking were all involved. What the people in the office work out, Lemi gets to implement in the tool shop. "Lemi with an i and not a y! Y would be Kilmister, the singer and bassist of Motörhead," the mechanic, whose real name is Rolf Lehmann, kindly corrects my notes. His workplace is plastered with posters of rock bands and festivals. "These are all posters from concerts I've attended," he says proudly as he tinkers with a device whose purpose I don't immediately recognize. "This thing here makes pot lids for the pressure cooker. It punches the holes for the lid. Currently it is in maintenance with me. After each completed production, I check the tools to see if they still work."

Tools here are not simple screwdrivers or hammers, but entire machines that produce thousands of lids in shifts from 5 am to 10 pm. They are so heavy that they are moved through the halls by forklift trucks and cranes. In a huge warehouse, they wait to be used in the factory or serviced in the tool shop, where Lemi has worked for 30 years. "I still like it," he says, in part because of the commute. He lives two minutes from the factory, he says, and not by accident. "When I started here, the old patron Jacques Kuhn - the inventor of the Durotherm - got me an apartment nearby. They belonged to the Kuhns and were almost all rented out to Kuhn Rikon employees at the time." At what rent he does not want to reveal. "Otherwise people will still be envious!".
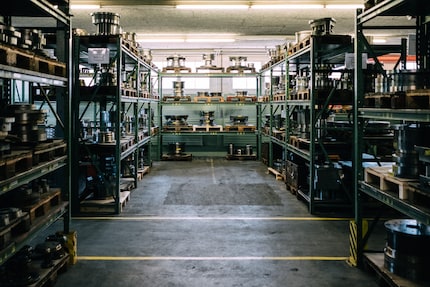
A life without computers and cell phones
The fact that the new lid design with the recessed handle works is also thanks to the rock fan with the black bandana. Designers and engineers can come up with the craziest shapes, but at some point they have to come off the assembly line. To do this, Lemi mills prototypes according to the engineers' and designers' wishes. All by hand. He has dealt with computer-controlled milling and drilling machines, so-called CNC machines, before, he says. "But that's not my thing at all. I don't own a computer or a cell phone." Instead of listening to Spotify, Lemi collects records, over 1200 of them, including real rarities.
My next stop is a production hall, where the polished blank is inspected by an employee in quality assurance. She taps the bottom with a small hammer and listens very carefully. "This load is going to Taiwan, which is a very delicate clientele," explains Production Manager Mathias Schneider. "There, people afford our pans as a luxury product and spend a quarter of their monthly wages on them. So it's our responsibility to deliver only the absolute best and most beautiful goods."
An extra sausage for Taiwan? "Of course not! But Swiss people inspect the pans a little less closely when they unpack them. When in doubt, everything that leaves the factory here has a 10-year warranty anyway and is flawless, regardless of whether it was produced for Taiwan, the U.S. or Switzerland," Schneider assures us as we look at the pans that have been deemed inferior. If the scratches hadn't been marked with a felt-tip pen, I wouldn't have seen them.
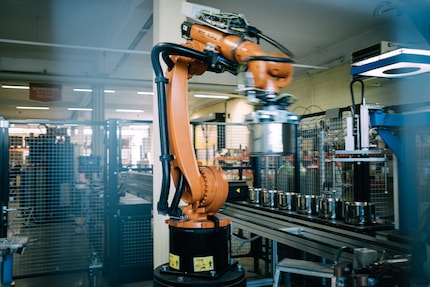
Only now is it decided which pan will become our blank. A robot arm grabs the polished blank, with a short crackle it welds on two knobs, which then protrude slightly from the side wall. In this case, it becomes a pot with a handle.
After the excursion into the arms of the robot, the blank comes back into the hands of humans. The handle must be attached to the pot. "Zurr" and "squeak", the employee does a short load test and the pan travels further on the conveyor belt.
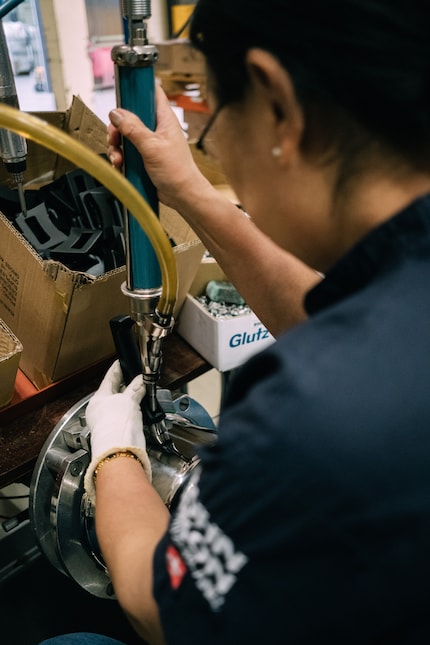
Gossiping and bussing while packing the pans
"We're already done, that's why we were at the Schnädere!", explains one of four women a little embarrassed, as we bring a cart with pots into the next hall. "No problem, as long as the work is done," the production manager replies with a wink. The four of them don't seem to hear that anymore. Concentrated and mechanical, they pack the pans, every move is spot on. Open the box, put in the instructions, steam the box around the pan, put the lid on top, close the box, put it on the pallet, then start all over again. Everything happens so quickly that I can't see which employee is doing which job. The boxes pile up higher and higher on the pallet until it is fully packed just in time for lunch and the four employees disappear for their lunch break.

We are still standing there, in the empty halls, suddenly everything is quiet. Lemi walks by, I notice the Pink Floyd T-shirt. "That's my favorite band," he says.
The song "Time" by Pink Floyd comes to my mind, where cacophonous clock chiming dissolves into a precise ticking and finally becomes an opulent composition. It's very similar with "Kuhn Rikon": first there are the wild ideas in industrial design, then engineers and toolmakers create the exact template of what such a pan should look like. Finally, a perfect "Swiss Made" product rolls off the conveyor belt in the factory with insane precision.
The new Durotherm from "Kuhn Rikon" will be available on Galaxus.ch in the fall. Here is a selection of other pans made in Rikon. The entire range is available here in the store
When I flew the family nest over 15 years ago, I suddenly had to cook for myself. But it wasn’t long until this necessity became a virtue. Today, rattling those pots and pans is a fundamental part of my life. I’m a true foodie and devour everything from junk food to star-awarded cuisine. Literally. I eat way too fast.