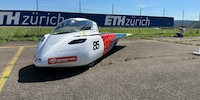
Background information
This solar racing car will be cleared to fly – but driving it is still tricky
by Martin Jungfer
Solar panels made in Europe, not China? Believe it or not, they do exist. For now. Swiss firm Meyer Burger hopes technological progress will help it survive the battle against its mighty Chinese competitors.
In a lot of people’s minds, Chinese products aren’t just low in price, but also low in quality. Products marked «Made in China» on Galaxus often come under fire in the comments section. However, the days when all China exported were weird-smelling, plastic dolls and wobbly feeding stations for pets are long gone.
The Chinese car industry is poised to overtake Europe’s – at least according to an increasing number of experts and business journalists. China’s a competitor in plane- and train manufacturing too. For a number of years, it’s also been the world’s largest producer of solar panels, which play a crucial role in the fight against global warming. In 2022, seven of the top 10 solar panel manufacturers were based in China, with Chinese firms taking every single place in the top five. At that point, companies such as JA Solar and LONGi Solar each had tens of thousands of employees.
In Europe, Meyer Burger is the only manufacturer of solar cells and panels left. The company dates back to the 1980s. Back then, it was producing saws for the manufacture of wafers – semiconductors used in both the microchip industry and the production of solar cells. As these silicon wafers were thin and, consequently, fragile, wire saws and a high level of precision were required. Something Meyer Burger was more than able to offer.
Forty years have gone by since Meyer Burger joined the solar business – and I’ve been given the opportunity to find out how the company’s planning to take on China’s industry giants. The first time I saw Meyer Burger’s highly efficient solar cells, they were attached to a solar-powered race car. It was summer 2023 and I’d been invited to check out Switzerland’s entry to the World Solar Challenge.
The ETH team opted for Meyer Burger’s solar cells because of their high level of efficiency. The factory even went out of its way to take cells from the production line that were a few tenths of a percent more efficient than others.
However, the cells aren’t actually manufactured in Switzerland. Meyer Burger produces both its cells and its panels in Germany. In Freiberg and Bitterfeld-Wolfen, to be exact. This is where I’ll be heading in my quest to find out more about the company. Located in the state of Saxony-Anhalt, the town has always been shaped by industry. In the Third Reich, goods essential to the war effort were produced there. In the GDR era, Bitterfeld was a chemical and mining town and was considered the «dirtiest town in Europe» in the 1980s (article in German). The chemical industry’s still present in Bitterfeld to this day, the companies occupying a site called «Chemiepark» or Chemical Park. I guess that sounds greener.
In 2020, Meyer Burger took over a factory belonging to the bankrupt firm Sovello AG in another industrial area located in Bitterfeld’s Thalheim district. Taking inspiration from Silicon Valley in the USA, a company called Q-Cells had set out to to build a Solar Valley in the area. Most of the companies have disappeared, partly because subsidies for the sector were cut in Germany, and because China rose to become the world’s solar giant – ironically thanks to massive state subsidies.
The Meyer Burger factory is on Sonnenallee (literally Sun Avenue). It’s a wide access road in a huge industrial area with swathes of undeveloped land. Big things were supposed to be created here. However, solar panel prices began plummeting in 2011 as the Chinese market kicked into gear. The firms of Solar Valley were suddenly no longer competitive and, within the space of two years, they gradually threw in the towel or were bought up by Chinese companies.
Today, life has returned to some of these giant factories. More specifically, to the one where Meyer Burger produces solar cells. The Swiss company manufactures the cells here, then sends them off to the Freiberg plant in Saxony, 150 kilometres away, where they’re assembled into solar panels. These panels primarily end up on the roofs of houses, offices or factories. Alternatively, they’re set up in motorway-side fields or on sunny mountain plateaus.
Meyer Burger takes pride in being one of the last European solar panel manufacturers. Jochen Fritsche, Production Manager at Meyer Burger’s Bitterfeld plant, gives me the grand tour. Row by row, step by step, the so-called raw wafers, i.e. the silicon slices cut from crystal, are turned into solar cells. A solar cell measures in at six inches square, about 16 centimetres. One hundred and twenty half cells are used in one panel, delivering an output of up to 400 watts. Meyer Burger is particularly proud of the fact its panels are more efficient than those of the competition. In fact, they can reach up to 21.8 per cent efficiency.
The difference in performance between cells is minimal. Ironically, this is down to Meyer Burger supplying its technology in the form of machines to solar panel manufacturers around the world, especially Chinese firms (until its change of strategy in 2020). Meyer Burger technology probably contributes to 90 per cent of all solar panels the world produces today.
Ever since Meyer Burger’s decision to both research new technologies and start producing them itself, the company hopes it has time to translate its technological progress into commercial success. Supplies of Russian gas have fallen since Russia invaded Ukraine in early 2022. Pretty good conditions for further investment in the solar industry. The fact that politicians are becoming increasingly critical of the West’s economic dependence on China’s solar industry should also prove advantageous for Meyer Burger.
Meyer Burger is still recording losses. Company executives recently announced that without state assistance, the firm would close its largest solar panel plant in Freiberg in the first half of 2024 (article in German). Production will instead be concentrated in the USA, where the Biden administration is promoting the development of the solar industry (article in German).
Without subsidies flowing, the battle against cheap, Chinese-made panels doesn’t seem winnable in the short term – even with ultra-modern solar cell production facilities like the one in Bitterfeld-Wolfen. Meyer Burger’s cells have a number of good selling points. Assembling the panels in its factory requires less water and fewer chemicals. What’s more, the process is done at relatively low temperatures of around 200 degrees Celsius, meaning less energy is required. Any electricity the factory does consume is generated completely sustainably. In addition, cells manufactured by Meyer Burger using heterojunction Smartwire Technology don’t contain lead, a material that proves problematic when the cells are recycled at the end of their service life of at least 25 years. As Jochen Fritsche explains, Meyer Burger’s modules are actually «fully recyclable.» Chinese ones, he says, eventually «just get shredded».
Meyer Burger produces enough cells for around 8,500 panels per day. It’s able to scale up production when demand increases. A typical single-family home would need 15-30 panels. When it comes to large solar fields on flat ground, several thousand are required. The fact that Meyer Burger modules have a higher energy yield means greater quantities of electricity are generated. As a result, the initially higher investment required to buy the panels quickly pays off. One example of a successfully completed project is the family business Ferag AG, based in Hinwil in the canton of Zurich. The company’s installed over 2,600 panels on its factory building.
If you’re interested in the physical and chemical details of the production process, I’d recommend this video by Money for Future:
This video explains the theoretical basics about how solar cells work.
A sense of optimism’s in the air inside the 40,000-square-metre factory building in Bitterfeld. And it’s not just because the employees are wearing T-shirts printed with slogans such as «Work for a vision». As I was walking through the building, I could feel their enthusiasm, inventiveness and pride.
That being said, it’s also become clear in recent weeks that the 70-year-old Swiss company is struggling to survive. It’s counting on quality, the «made in Europe» selling point and the energy transition to get them through. And as the David battling the solar Goliath of China, it needs political support. Otherwise, a recent editorial published in the «NZZ am Sonntag» newspaper might just prove prophetic. Meyer Burger’s panels produce higher yields and are more durable than panels made by competitors in Asia, but:
Nevertheless, instead of coming out on top, Meyer Burger has turned into an illustration of a brutal truth. In the market, it’s not always the best that prevails. More often than not, it’s the mediocre.
In the interests of transparency: my family and I have a PV system installed on the roof of our detached house. It’s composed of panels made in China. After my visit to Meyer Burger, I briefly considered having the panels replaced. Doing so, however, wouldn’t be financially viable. Instead, I spent a modest, three-figure sum on shares in Meyer Burger AG. The stock price has fallen drastically since then. In publishing this article, it’s not my intention to influence that stock price, nor do I believe it’s realistic to do so.
Header image: Meyer Burger AGJournalist since 1997. Stopovers in Franconia (or the Franken region), Lake Constance, Obwalden, Nidwalden and Zurich. Father since 2014. Expert in editorial organisation and motivation. Focus on sustainability, home office tools, beautiful things for the home, creative toys and sports equipment.