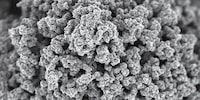
Background information
2018 is bound to be the year of the revolutionary battery
by Aurel Stevens
The start-up XNRGI is said to have succeeded in making lithium-ion batteries cheaper and more powerful. This could enable electric cars to cover distances of over 1000 kilometres on a single charge.
Currently, electric vehicles can cover a distance of between 350 and 450 kilometres, depending on the manufacturer. Tesla leads the way here and is the exception with up to 600 kilometres. However, a start-up from Portland, Oregon, is now said to have found a way to more than double this range. According to XNRGI, by optimising the design of lithium-ion batteries, electrically powered vehicles should be able to travel much further as early as next year.
First things first: this is not about the new wonder battery. Our colleague Aurel Stevens has already made it clear that this is still a distant dream of the future.
It is also not uncommon for someone to claim to have discovered the revolution in the battery business. In this case, however, the situation is somewhat different. This is because XNRGI can boast financial support from the US government and patents.
According to Digital Trends, the Americans are focussing on the so-called Powerchip battery technology, for which the company already owns a large number of patents and has applied for more. The US Department of Energy also believes in the start-up's promises, as it is supporting the researchers with funding. CEO Chris D'Couto believes that his technology has solved all known problems with lithium-ion batteries. The two biggest obstacles are the risk of fire and the highly expandable energy density.
According to XNRGI, the solution is simple: instead of trying to invent or develop something completely new, they have transferred a functioning technology from chip manufacturing to battery production. The start-up relies on so-called wafers from the semiconductor industry - circular or square silicon discs with a thickness of around one millimetre.
As XNRGI works with older wafer generations, D'Couto says that the dwindling supply and rising price of silicon is not a problem. During production, the Americans drill up to 160 million mini-holes into a twelve-inch wafer disc. One side of the disc is conductive, the other is not.
After production, the wafer is to be used in the anodes of the battery. This is where the electrons collect when the battery is charged. To date, graphite has often been used for this purpose, but this has an energy density ten times lower than the new three-dimensional and holey silicon wafer technology. In addition to the safety aspect, this should also extend the service life by three to five times.
The CEO of XNRGI says that an electric car battery manufactured according to the XNRGI principle can be charged to 80 per cent in just 15 minutes. In addition, the range can be increased by up to 280 per cent, i.e. almost three times. This would allow electric cars to travel up to 1200 kilometres before the battery needs to be recharged.
Drivers will have to be patient, however. According to XNRGI, the technology will be used in electric scooters, drones and robots as early as next year, but will not be able to be installed in electric cars on a large scale until 2024.
When I'm not stuffing my face with sweets, you'll catch me running around in the gym hall. I’m a passionate floorball player and coach. On rainy days, I tinker with my homebuilt PCs, robots or other gadgets. Music is always my trusted companion. I also enjoy tackling hilly terrain on my road bike and criss-crossing the country on my cross-country skis.